Equipment Throughput Case Study
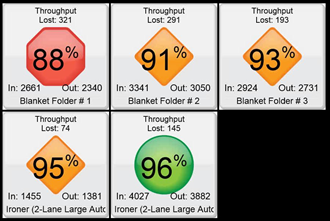
The Problem: A commercial laundry lacked visibility into how many labor hours they spent reprocessing stains, tears, and drops from their equipment.
The Solution: In less than two weeks an equipment throughput solution allowed the plant to visualize the impact these stains, tears, and drops were having on the operational performance. An increased focus on improving equipment throughput, enabled the plant to eliminate over 1,170 labor hours spent reprocessing stains, tears, and drops over the course of the year (an estimated savings of $14,713).
After installing SpindleLIVE in 2018 and seeing first hand the power data can play in improving employee productivity and operational performance, a commercial laundry in the United States was looking to get a better understanding of how their equipment was performing.
In December 2020, they decided to install Spindle's Equipment Throughput solution on their large piece ironers and folders that would measure the amount of product fed into a machine against the amount of product that exited the machine through the stackers.
By installing the Equipment Throughput solution, the company gained access to:
- Real-time dashboards to their production employees that would allow them easily spot possible issues with equipment or operator errors.
- Historical reports that would allow management to identify pieces of equipment that are continually having issues or trending in the wrong direction.
A deep dive into the numbers
After a few weeks with the equipment throughput solution in place, the team was able to establish a baseline for which pieces of equipment would need their attention the most. They decided to focus on blanket folder #1 (the teal line in the graph above) and blanket folder #2 (the black line) which during the week of February 20th, had a throughput of 85% and 79% respectively.
A snippet of the plant's throughput report for the week of February 20th
In just one week, the plant identified over 17,000 stains, tears and drops on just these two pieces alone! Refeeding these 17,000 items would be the equivalent of an additional 43 labor hours a week (or over $28,100 in labor wages annualized). These numbers do not even take into consideration reprocessing the items from start to finish in the laundry operations.
Plan to Improve Equipment Throughput and Results
Empowered with the knowledge that something is wrong with these two pieces of equipment, but not knowing what, the team watched these two pieces of equipment carefully for the next two days. What they found was the clips on the equipment was dropping the items at an alarming rate.
After identifying the operators were correctly putting the items into the clip - they made some programming adjustments to the clips and watched again the next day.
These improvement's allowed the team to raise the throughput significantly in just 2 weeks. Looking at the throughput report for the week of March 6th, the team improved throughput on Blanket Folder #1 by 6% and Blanket Folder #2 by 11%.

A snippet of the plant's throughput report for the week of March 6th, two weeks after focusing on improving equipment throughput.
Even though they processed only 127 more items the week of March 6th, they were able to reduce the amount of items needing to be reprocessed by 8,941 pieces! That's the equivalent to saving 23 hours or $283 for the week and $14,722 annualized!
A snippet of the two week equipment throughput trend line
What's Next for the Plant?
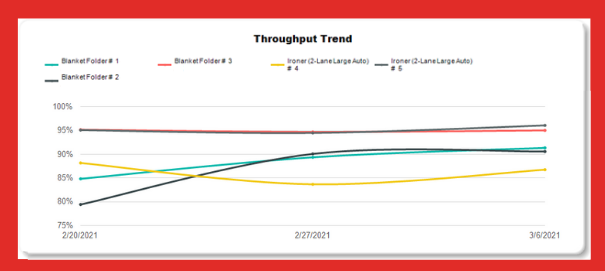
Recognizing these savings are just the beginning, the plant is setting a goal to improve all their ironers and folder's to have a throughput of 95% or more in their plant. The equipment currently performing under 95% for the week of March 6th is costing the plant an additional 21 hours or over $14,000 if the trend continued for the year.
Equipment Throughput Standards in the Industry
While industry expectations are typically between 3-6% of stains, tears, or rejects losses on average, we've found that most hospitality and healthcare operations far exceed this benchmark. Typical values we see are between 12-15% loss in throughput when plant’s first begin measuring it. Depending on the size and hourly wages in your plant, this can equate to losses of over $50,000 in labor costs alone!
If your interested in learning more about how Spindle's Equipment Throughput can help your organization, we'd love to hear from you. Reach out below.