How to Improve Your Commercial Laundry Plant Using Software
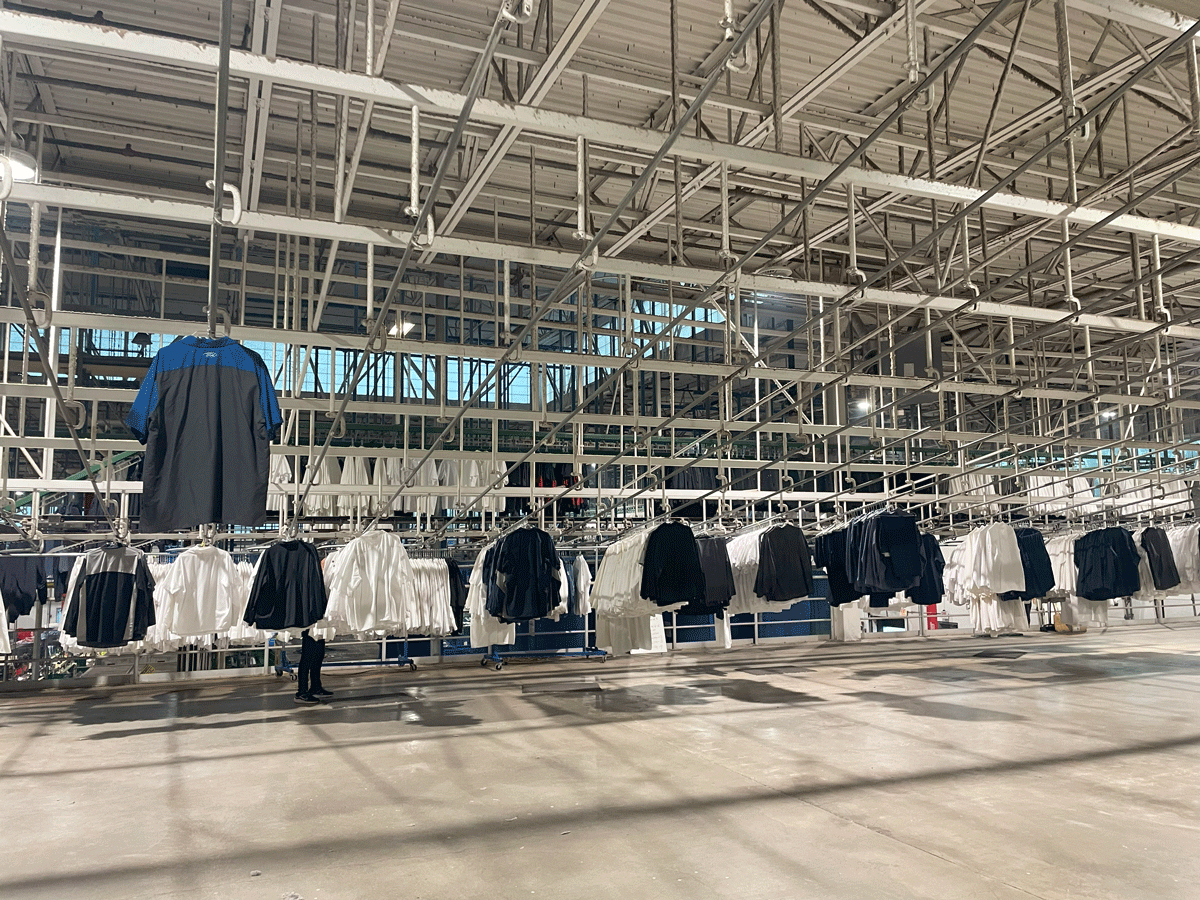
We've previously covered how big of an impact unplanned downtime can have on your commercial laundry plant, and how better commercial laundry maintenance can be a profit center for you.
In order to take advantage of those hidden pockets of revenue, you need visibility into what's going on with your equipment.
Third-party software applications, like Spindle, can help you keep track of your equipment health, maintenance tasks, and equipment historical data and trends. Armed with that information, you can have a window into what might happen to a piece of equipment ... before it even happens.
In this article, we'll review the key ways Spindle commercial laundry software can help you keep tabs on your valuable equipment and tackle preventive maintenance effectively.
The Value of Data: Visibility
As mentioned above, visibility is key when it comes to maintaining the many pieces of equipment you have in a plant.
In a word, that means data.
With data, you're not guessing, speculating or hoping (e.g., delaying or ignoring maintenance because you're banking on a piece of equipment continuing to operate properly and without disruption).
Data gives you visibility: it's like a pair of night-vision goggles in the dark. Based on historical trends, is a piece of equipment likely to break down and need maintenance soon? With data, you can address it and slash your downtime as a result.
As we noted elsewhere, unplanned downtime is prohibitively expensive. From emergency maintenance to labor costs, unplanned downtime will cost you much more than routine maintenance will.
While the cost of downtime can vary wildly by industry and by the size and type of plant, the cost of downtime in manufacturing comes in at $260,000 per hour on average, according to one estimate.
Again, while downtime might not cost you quite that much at your commercial laundry plant, it's probably costing you a lot more than you'd want.
Six Ways to Optimize Your Commercial Laundry Maintenance Efforts with Spindle Software
So with the understanding that unplanned downtime is debilitating for your plant, and that good commercial laundry maintenance can be a profit center for you, what do you do next?
How do you reduce unplanned downtime and take advantage of hidden cost savings?
Here are five ways Spindle can help you optimize your commercial laundry maintenance program:
Address Equipment Bottlenecks ... Before they Happen
A piece of laundry -- whether it's a napkin, a towel, a garment, etc. -- goes on a long, multistage journey through a commercial laundry plant. Sorting, washing, drying, packout ... the bottom line is, there are a lot of stages where things could go wrong.
Think of a car accident on your morning commute to work. A really serious accident might lead to the shutdown of one or more lanes. As a result, the total sum of cars on the road has to find a way to squeeze by the accident site in fewer available lanes.
Traffic still flows, but rather than in a speedy and orderly fashion, it moves at a trickle.
Now take that and imagine the commercial laundry plant. If a certain piece of equipment at some point in your process flow breaks down unexpectedly and remains down for an extended period of time, your entire operation is hampered. You likely have some redundancy, so you'll be able to continue production using other machines. Like the traffic example, though, you'll then have to process the same amount of laundry with fewer available equipment pieces.
In short, you've got a bottleneck on your hands.
Spindle real-time operations software gives you insights into your operation so you can quickly address any problem areas.
Aid Major Economic Decision-Making
If you're wondering whether you need a new piece of equipment to meet demand, Spindle can help with that, too.
Spindle dashboards can show you easily digestible summaries of your equipment utilization rates, meaning you can see if you're getting the most out of what you've got. If the answer is yes, then you might then look into committing the funds to new equipment.
If you aren't, you might then save yourself the capital expenditure and instead focus on improving your existing equipment efficiency.
Visualize Your Equipment Effectiveness
You can't address a problem if you don't know it exists.
Spindle data helps you visualize your Overall Equipment Effectiveness (OEE) to see where capacity losses are happening.
You can even get out your magnifying glass and look deeper to identify losses at the equipment and lane level.
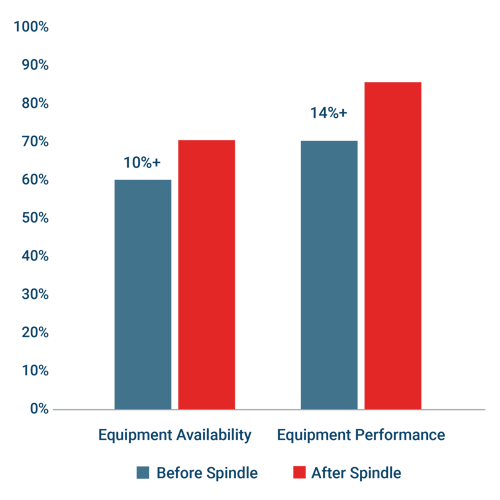
Increase Visibility into Your Maintenance Workflow
There are a lot of things going on in your plant at a given time. Without some help, it's nearly impossible to keep track of it all.
Spindle can help you keep track of where maintenance employees are by seeing which piece of equipment they're logged into.
Even better, you can have all your maintenance tasks in one place. No need for pen and paper or word-of-mouth updates. A handy Spindle maintenance calendar serves as your one-stop shop for updates on all maintenance tasks at your plant, whether they're pending initiation, in progress, completed or something in between.
Know Your Equipment's Full History
With Spindle, you can have access to the full range of historical data for any piece of equipment.
Think of it like that equipment piece's story. By understanding what's happened to that equipment in the past, you can have a better sense of expected downtimes and adjust your maintenance calendar accordingly.
Manage Your Parts Inventory So You're Ready
In reality, even the most diligent preventive maintenance program can't stop 100% of all equipment issues. Sometimes, equipment breaks down or a particular part of the equipment ceases to function properly.
That means you need spare parts. In this era of fluctuating supply chain reliability, you want to make sure you have the parts you need on hand so you're not facing an extended period of downtime while you wait for a part order.
Spindle helps you keep track of your parts inventory, identify preferred vendors and, if you have multiple locations, keep track of part availability across all of your sites.
On the other hand, you can adjust in the other direction, too, by using the data to identify parts you already have in sufficient supply, saving you money on unnecessary purchases.
Summary
Bottom line, if you're tracking maintenance data in Excel spreadsheets or even pen and paper, you're likely not getting the most out of your equipment.
Real-time data, collected and presented for you in a user-friendly interface gives you the visibility into what's really going on with your equipment.
Armed with that data, you can see into the future and stop problems before the start and, ultimately, save money in the process.
This article outlines just some of what Spindle can do for your commercial laundry maintenance efforts ... but it only scratches the surface of its potential.
Empower yourself and your team to make your commercial laundry maintenance program a gamechanger for your plant.
Request a demo of Spindle to see for yourself what's possible.