3 Tips to Improve Your Laundry's Overall Efficiency
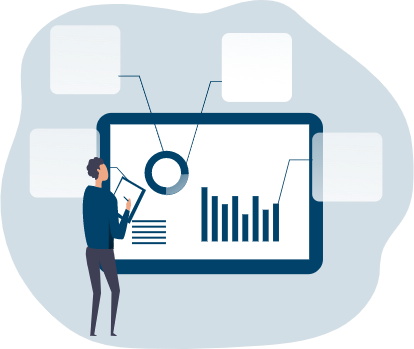
Laundries are littered with data. An American Laundry News article states “Data is a topic that many in our industry are still lacking to grasp and efficiently make use of”. Numerous opportunities for collecting data are overlooked or deemed too complicated. When the data is collected, managers often have a hard time acting on it due to the timeliness and integrity of the data.
“Spindle’s true value is in the immediate visual feedback to the end-user and the drastic reduction in labor previously required to manually collect data and provide one-on-one feedback from the management team." - Spindle Customer, Operations Manager
Spindle helps by automating the collection of data and providing managers with actionable insights into their plant. Since you’re no longer spending time running around collecting data, you’re able to quickly look at Spindle’s real-time dashboard and spend time managing the areas that truly affect your operation's bottom line.
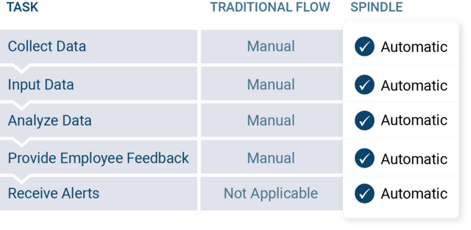
Below are 3 ways plant managers use Spindle to increase employee efficiency:
1. Identify Best Practices, Then Share Them!
"Our soil sort production was in the 60 percentile and now we increased it to 100% - just by introducing a new standard operating procedure." - Rebecca Koury, POS
A LEAN operation is one that identifies best practices and shares them with others. The teams that are constantly looking for “the best way” to do each activity ultimately become elite laundry plants. Spindle helps Plant Mangers identify best practices on each activity within their laundry operation. Here is an example of how a very efficient laundry plant uses Spindle:
A plant manager identified productivity inefficiency on garment hanging was costing his plant hundreds of dollars a week. Spindle’s dashboard showed that employees were wildly inconsistent with productivity ranging from 35% to 115%. He went to the floor and learned how the employee with 115% productivity was beating the expected standard processing time.
The employee shared her technique with the manager and then trained the other employees. Not only was there an increased efficiency gained from standardizing the best practices, it increased the morale of all employees -- especially the employee who was recognized for her great technique.
2. Using a Visual Workplace Improves Productivity by 5-10%
"The PPOH improvement has exceeded our expectations, but more importantly our employees can feel what success feels like because of the real-time feedback and that is priceless.“ - Vaughn Austin, Aramark
Many recent polls are finding that more than 70% of workers are not engaged at work. With the increase of
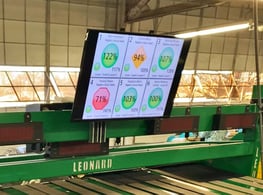
Enter Spindle’s visual workplace. Our software accurately captures real-time performance data and displays the results to your employees using easy to interpret shapes. This on the spot feedback not only empowers the employees to know exactly where they stand against their performance goals, but also gives the plant manager instant insight into which areas are performing well and which need their attention.
We’ve found simply adding this visual feedback leads to an increase in productivity by 5-10%.
3. Right Seat on the Bus
“I have been able to find where people are stronger. They may be weak in an area and by moving them somewhere else, they improve. I had someone on the bulk fold area and she wasn’t doing well. I moved her to the press area and her number shot up to 96% efficiency.” – Matthew Smith
Everyone has their strengths and weaknesses. For your laundry to operate as efficiently as possible, you need to be sure everyone is playing to their strengths. Spindle gives you access to previously untracked metrics of your labor force, allowing laundries to easily uncover where these strengths are for each employee.
For instance, one laundry had an employee whose average overall efficiency was just 69%. The PM used Spindle to discover that while she was a low performer in areas such as Soil Sorting and Ironing, she was excellent at Automated - Bagging. The PM made her primary task Automated - Bagging moving forward and her overall efficiency bumped up to 85% in the following weeks.
In this industry where hiring and retaining employees is becoming more and more challenging, companies have a competitive advantage when they can turn low performers into high performers.
|