How to Cut Production Time and Costs

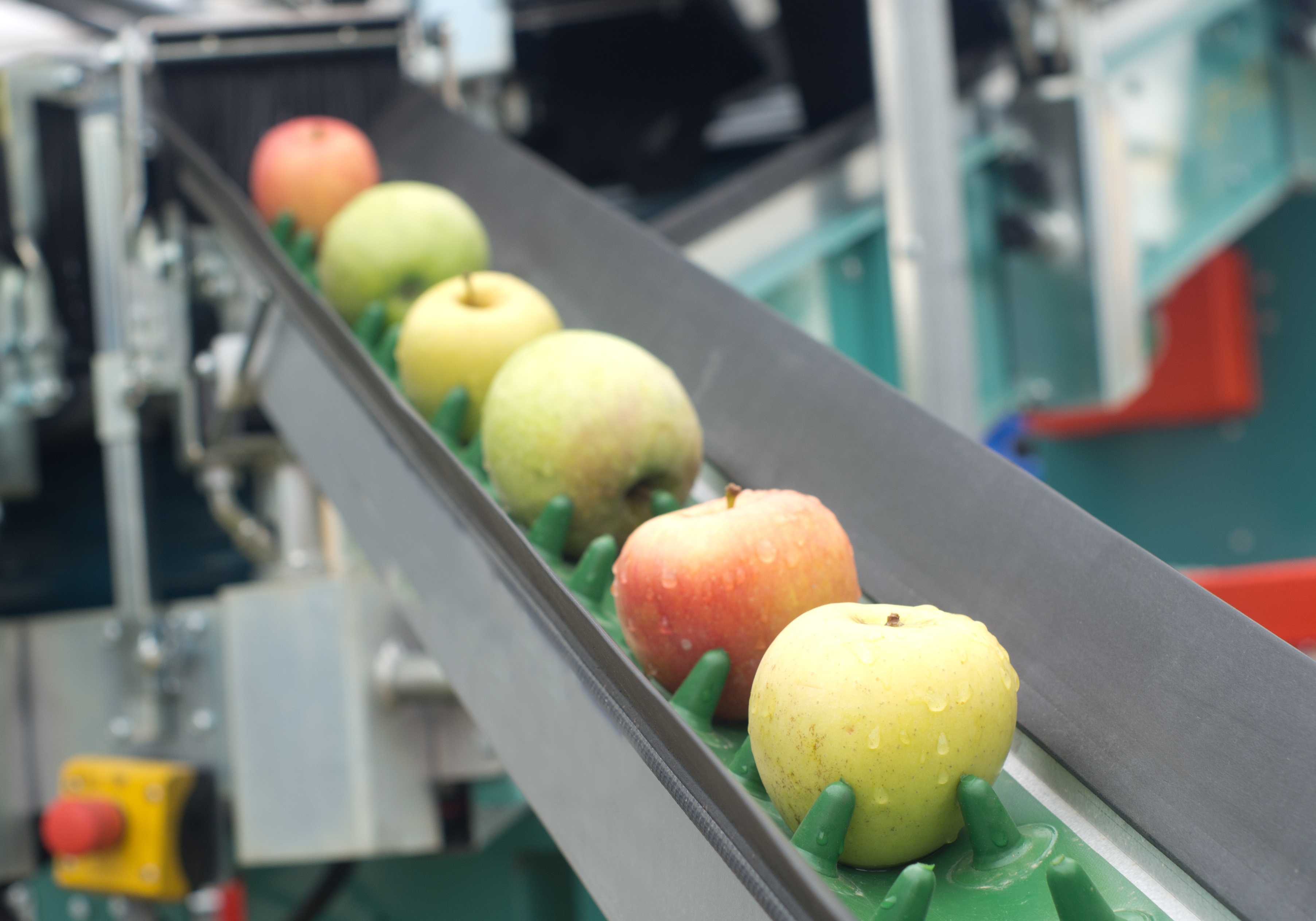
How to Cut Manufacturing Costs
As a manufacturing plant manager your goal is to run a successful and efficient operation. We’ve put together some ideas to help you cut manufacturing costs by focusing on four areas of your operation: Labor Costs, Energy Consumption, Material Costs, and Capital Investment.
Reduce Labor Costs
Boosting employee productivity and implementing efficient process flows are effective ways of getting more done with less. Whether that is growing your business faster than you grow your workforce or having the flexibility to make adjustments if business dips. In either case, an optimized workforce and workflow will lead to higher profits, lower relative costs and improved employee morale.
Although labor costs can be reduced in ways such as lowering employee wages, hiring cheaper unskilled workers or reducing the number of employees, this can be detrimental to employee morale, have a negative impact on your company’s reputation and end up costing you in the long run.
With Spindle’s Visual Dashboard you can monitor employee productivity and feedback in real-time through the Supervisor and Manager dashboards. Whether you’re at your desk or on the floor these dashboards are conveniently available on both desktop and mobile.
Employees are effectively engaged with Visual Dashboards at each workstation. The workstation Visual Dashboards clearly display production goals and standards and allows employees to view their performance and efficiency levels.
Reduce Energy Consumption
In the United States, over $100 billion is spent annually powering manufacturing plants. Improving energy efficiency not only reduces costs, waste and emissions, but gives you a competitive edge with increased earnings. For many sectors, a well-run energy program can reduce energy costs by 3% to 10% annually.
Spindle’s Water and Energy Plugin monitors natural gas, water, electricity and other meter readings and alerts for energy consumption or process control issues. Trending and alerting are combined with intelligent metrics to show issues as soon as they arise in real-time and allow for swift attention, especially when compared to traditional diagnosis (i.e. weekly readings or a monthly utility bill). The Spindle Analyst team can also help with benchmarking and consulting on consumption by piece of equipment or with ideas to improve processing efficiency.
Reduce Material Costs
In order to control material costs, conduct an audit to determine which materials are vital to the function or quality of your production. Analyze your procurement methods and cut unit costs by purchasing materials in large lots. Seek more efficient ways to use less material in the manufacturing process. It is also important to provide documentation and proper training to employees to reduce the amount of material scrapped during production.
SpindlePRO keeps your equipment running well with emergency and preventative maintenance tracking and dashboards that allow for rapid response to equipment and process issues. Requirements features make sure the right products are being made for the right customers at the right time. Spindle also tracks product rejects and quality issues that cost money in reprocessing or scrap.
Invest in Capital
You’ve heard the expression; sometimes you’ve got to spend a buck to make a buck. Investing in equipment that makes your manufacturing process more efficient can lower the production costs overtime.
Spindle allows you to monitor all of your existing equipment in real-time, ensuring that each is being used for maximum productivity and efficiency.
Installation of Spindle is quick and organized. As a leading developer of operations management software, we strive to bring personal service to the software equation. Spindle’s Analysts and Consulting teams can benchmark equipment performance and recommend improvements to process flow and operating procedures. We are committed to providing our customers the tools needed to proactively diagnose and correct labor, equipment and utility deficiencies.